Die Keramikbeschichtung
Die Oxide verschiedener Metalle werden allgemein als Keramik bezeichnet. Die gängigsten keramischen Beschichtungen sind Aluminiumoxid (Al2O3), Chromoxid (Cr2O3), Titanoxid (TiO2) und Zirkonoxid (ZrO2). Sie unterscheiden sich in verschieden Punkten, wie Temperaturbeständigkeit, elektrische Leitfähigkeit, oder Säure – und Laugenresistenz.
- Chrom-, oder Titanoxid zur Wärmeabstrahlung, z.B. in der Luft-, und Raumfahrt
- Zirkon-, oder Aluminiumoxid zur Wärmeisolierung, z.B. in Raketen-, und Düsentriebwerken
- Zirkonoxid als Wärmedämmschicht in Kolben von Dieselmotoren, für Ventile und Zylinderköpfe
- Chromoxid für dichte, korrosionsbeständige Schichten in Pumpendichtungen oder Verschleißringen
- Aluminiumoxid für Anwendungen in der Textil- und Synthetikfaserindustrie, wo verschleißfeste Oberflächen gefordert werden, z.B. Fadenführungsrollen
- Thermofühler verschleißfest mit Chromcarbid oder Thermoschockbeständig mit Zirkonoxid beschichten
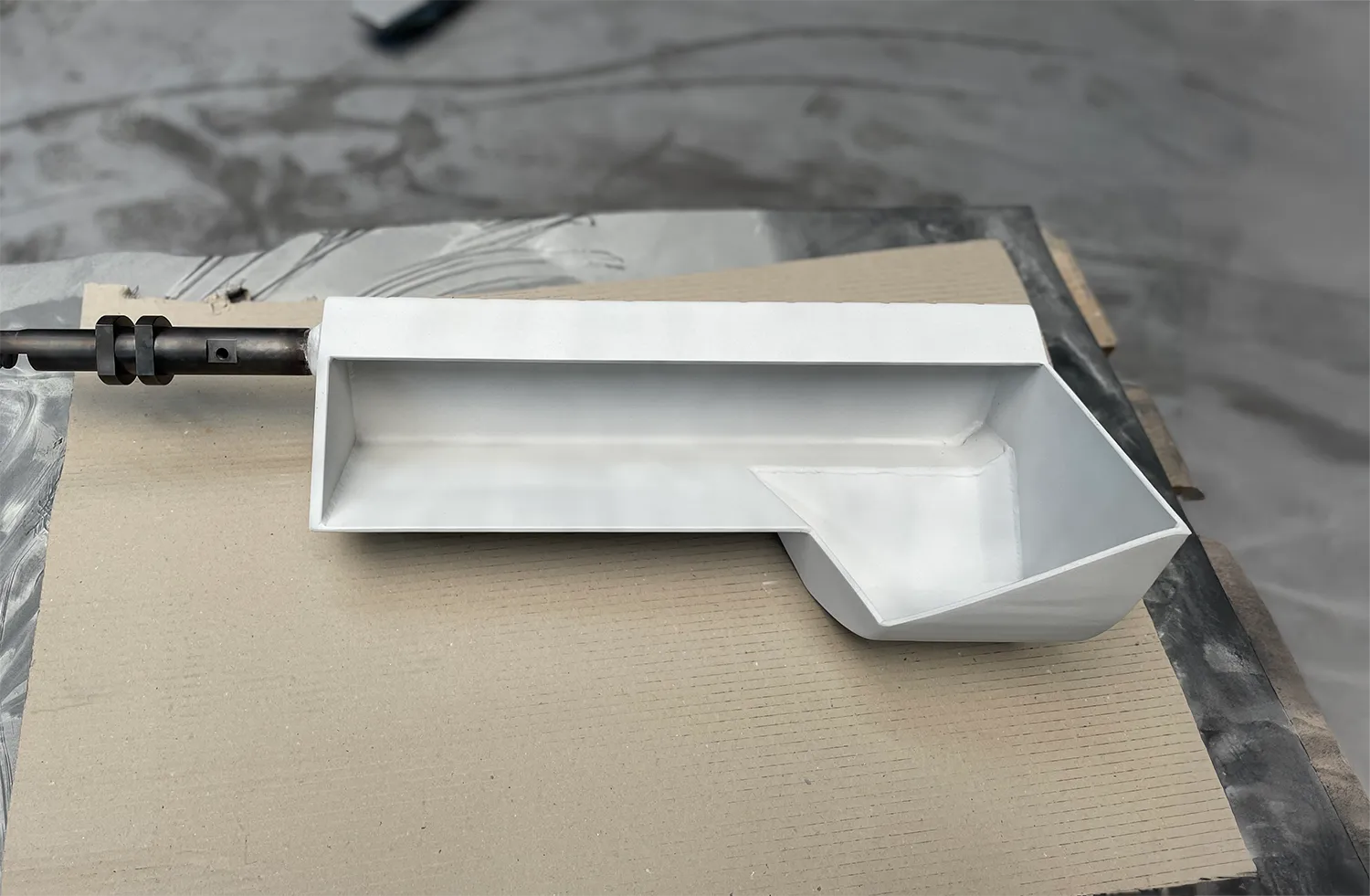
Gießloeffel_keramisch_beschichtet_zur_Vermeidung_von_Anhaftungen_durch_Al-Schmelze
Gießlöffel keramisch beschichtet, zur Vermeidung von Anhaftungen durch Al-Schmelze
Vorteile einer Keramikbeschichtung
Verschleißfest
bis zu ca.900 °C
Elektrisch
isolierend
Beständig gegen Säuren, Laugen und Alkohol
Weitere Eigenschaften der Keramikbeschichtung
- Hitzebeständig bis ca. 1600 °C (in Abhängigkeit von den Betriebsbedingungen)
- Erosionsbeständig über 845 °C
- Thermoschockbeständig
- Beständig gegen Heißgaskorrosion in schwefelchlor- und natriumhaltiger Atmosphäre
- Geringe Herstellungskosten der keramischen Schichten
Weitere Anwendungsbeispiele